LoCal Homes for Local People...
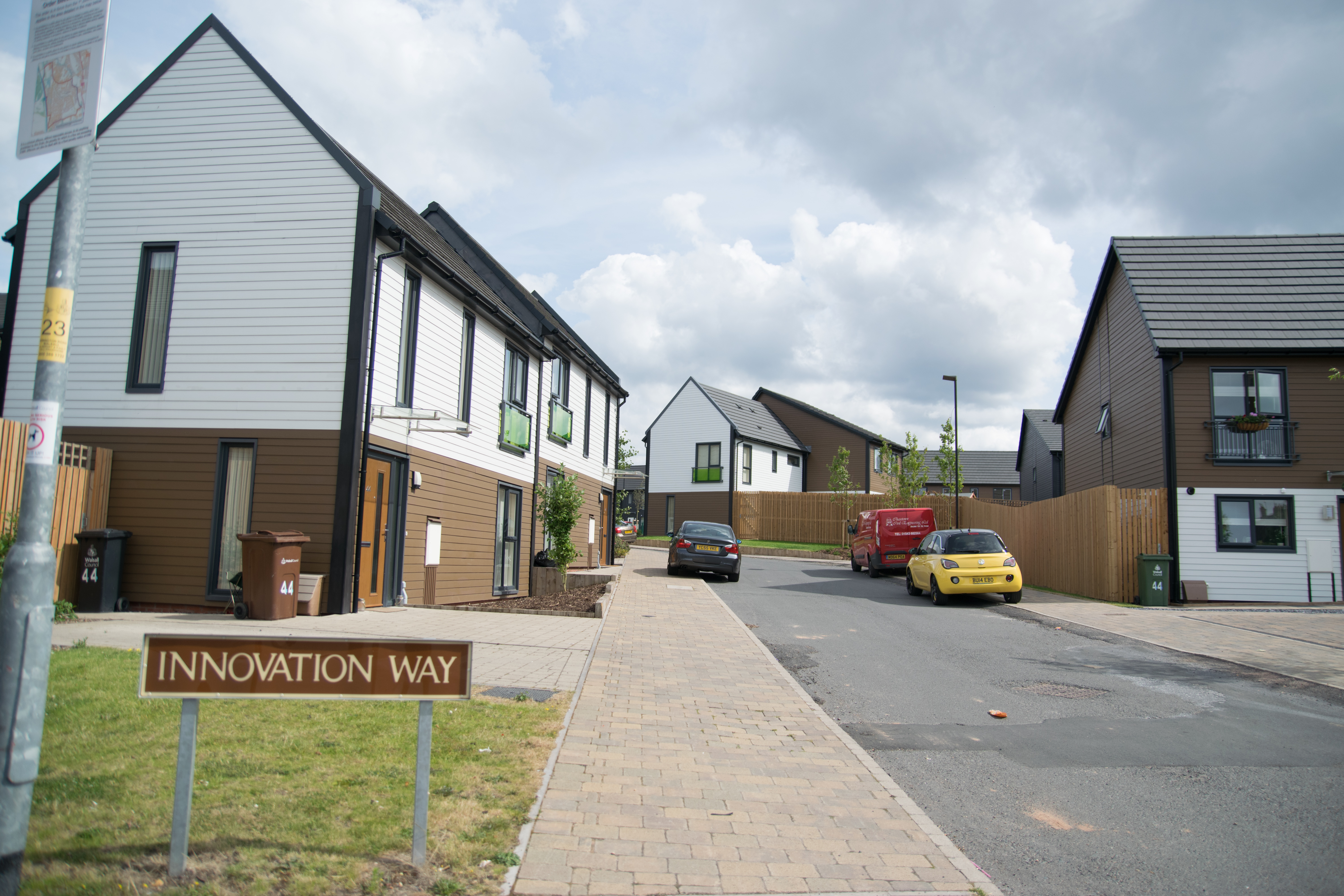
The latest in our series of blogs focussing on innovative approaches to the delivery of housing focusses on the model being undertaken by LoCal Homes, part of Accord Housing Association, a major housing and social care provider, who work in the Midlands and manage 13,000 affordable homes and social care to 80,000 people.
I am met in Walsall, where the LoCal Homes factory is based, by John Bedford, Accord’s amiable Director of Project Development, who heads up the project. The name, LoCal, John explains, is a contraction of Low Carbon Homes Built by Local People for Local People. Theirs is a socially minded approach (the organisation is a registered charity) based on a model Accord’s Executive Director of Regeneration, Alan Yates, came across in Norway, while researching Modern Methods of Construction in 2004. The Norwegian factory (https://www.hedalm-anebyhus.no/) has produced panelised timber framed homes for over 50 years and Accord was struck by the quality and pace of their approach. Following a factory visit by Accord and customer representatives, the organisation initially ordered 29 homes from the factory, dipping their toe in the water, and was taken aback by their popularity. They ordered more, but it was clear that to meet demand in an efficient manner, Accord would need to replicate the Norwegians’ approach. Working in partnership with Walsall Council, who were recipients of a healthy EU grant to produce more jobs in their borough and under Accord’s directive, John and his team duly established a factory at a cost of approx. £870,000 (including machinery), which manufactured its first homes in 2012.
John explains that the initial vision was initially to supply the Association’s own development programme (they now put £15 million a year of their Affordable Homes Programme, the UK’s SHG programme, through the factory), but that the model has proved extremely popular and they now have agreements in place with a number of different housing associations and local authorities to provide homes, with between 200-400 homes on order currently. The factory is modelled to break even at a competitively low level, so the potential to generate income from their output and reduce the cost per unit is high (though John is keen to stress that LoCal Homes runs on a social enterprise basis, with any surplus ploughed back into the business).
They are now at the point where, as well as manufacturing homes, they are keen to offer their services to others, as consultants. The ‘Factory in a Box’ concept offered by LoCal Homes is likely to be of significant interest to CHC members. For a fee, Accord will set up a factory for you, including recruitment and training of staff (from within the locality of the factory). One of the really attractive elements of this approach is that, over time, they will develop a network of linked factories, able to share excess production. They are currently in talks about this model with a consortium made up of a number of housing associations and the local authority in the South West of England, perhaps providing a blueprint of how CHC members could work with LoCal Homes. John suggests that prospective partners ‘think of it like a mothership model supporting a network of manufacturing outlets’.
It is important to note that they do not provide finished articles at LoCal Homes: their panelised system (not modular, John is keen to stress) manufactures closed-panel timber shells, the higher-quality version of which are their Eco 200 models: the Eco 200 homes are delivered to site in closed panels with the insulation in place, the external cladding fitted and windows and external door frames installed. The developer would be required to procure a contractor for groundworks and to complete the rest of the homes.
The cost of a home* includes transport (they stack neatly), design (John manages a team of in-house architects, Indesign, who use bespoke software to design the homes), windows, floor, roof trusses and erection. They can be delivered at no greater cost than a traditionally built home, at current levels of production (200-300 homes per year), but due the high quality of materials chosen LoCal Homes have achieved 28% greater thermal efficiency for less than a 5% premium. By constructing these homes with their own construction services team, Accord have reduced build costs by 10%, building higher quality homes at lower cost. As with all factory production, achievement of cost efficiency comes with increased production. Crucially, the homes are fully mortgageable – Accord sold 17 on their first development – and approved by the CML and LABC
Quality, as mentioned, is high – John says that their default position is to over-engineer all aspects of their product, with 200mm of insulation in the wall panels, the Eco 200 homes achieve a 'U' value of around 0.18 as opposed to 0.35 under current UK building regulations. This means low heating bills: experimenting with batteries in the homes, John’s team has managed to achieve an average £37 per month duel-fuel bill for a family of 5 in a 3-bed, 3-storey house. In terms of fire resistance, again the response is very impressive: the Local Homes system has been subject to fire test in laboratory conditions. A report on the test, undertaken by Warrington Fire found that system performed well in the 60 minute fire test and that after 72 minutes the system was still structurally sound. They have produced homes with sprinklers, although this is not standard, and can do so again. Indeed, their design process can be flexible to pretty much any needs (‘as long as they don’t want round buildings’) and there is no pattern-book, as such. Instead, the in-house design team can reproduce what they’ve done in the past, or produce new designs, as needed.
As well as providing high quality products, the LoCal Homes method means rapid on-site development. They have erected a home in just one day before, though this is unusual – normally, a team will work on a row of homes at a time, achieving water tightness in an average of two days per home. The homes are manufactured in a single day in the factory too.
The factory is an impressive space, staffed by a team of 12 local workers, who, John assures me, operate at an extremely high level of efficiency (just 3% of the timber they use is wasted). Jobs in the factory include hand-packing the Rockwool insulation, meaning that the homes are able to achieve a very high density of insulation. Working one shift, 5 days a week, the team can manufacture up to 275 homes a year from this factory although they are currently planning to move, in order to increase output to up to 1,000 homes per annum.
The timber the factory uses currently is imported from Scandinavia, for reasons of quality (they demand a 19% humidity level, which is most readily achieved by using Scandinavian FSC certified providers) but John is open to discussion with Welsh timber providers, accepting that the treatment needed to get Welsh timber to the same standard is likely to add to the cost.
One of the highlights of the trip is a tour of an estate directly over the road (‘Innovation Way’) which is comprised of over 100 homes built by LoCal Homes. The homes are attractive, coming in a range of shapes and sizes, including family homes, a modest block of affordable flats and adapted homes for disabled people. Customers, apparently, love them, as reflected in low turnover. The level of attention to detail of the properties is high; one particularly unusual roof-angle is explained as being the angle at which to extract maximum efficiency from the photovoltaic panels attached.
“It’s not the whole solution to providing affordable homes” says John, “but it’s 80% of the solution”.
* Cost withheld from this article for commercial reasons, but can be disclosed by LoCal Homes on request